Tools of the Trade: A Look Inside My Turning Setup
- Eric
- May 7
- 3 min read
Updated: Jul 13
Out here in the Smoky Mountains, just beyond the snowy view from my front porch, you’ll find my small workshop. It’s not fancy—just a quiet space where the hum of tools meets the rhythm of hands and heart.
People often ask what I use to craft the pens I make here at Mountain View Turnings. So today, I thought I’d take you behind the bench for a closer look at the tools that bring each piece to life.
Each item turned is unique, though I can come close to an original, each one has it's own shape. Hand turned art is special as no one else would have the same exact item. The wood, either already cut into a 3/4 x 3/4 x 6 inch solid blank or as a rough board that is planed and cut down to a turning blank ready for me to shape it. Acrylic blanks come either pen blank size or spindle turning size.
The hardware is ordered by me from trusted US suppliers, the "bodies" are turned by me and the finished item is assemble by me. The finishes I put on, are either a lacquer, friction polish, or a CA (Cyanoacrylate Glue) finish. Polished, closely examined, and if I approve, put up for sale, or given to family and friends.
I enjoy what I do. If I sell something, I stand behind it. If you buy an item from me, and have issues with it, contact me and we'll work it out. I use some of things I make, and they have not failed me, I want the same for you.
My Lathe: The Heart of the Workshop

At the center of everything is my Turncrafter Commander 10-inch Variable Speed Midi Lathe from Penn State Industries.
It may not be the biggest lathe on the market, but for me, it’s been a steady workhorse. Reliable. Consistent. Tough enough to handle everything I’ve asked of it so far. It runs smooth, adjusts with ease, and lets me focus on what matters—bringing each item to shape with care.
I’ve turned dozens of items on this lathe, and every time I power it up, I’m reminded of how far a good tool can take you when paired with patience and practice.
Chucks & Add-Ons: The Details That Make the Difference
Depending on the stage of the project, I switch between a few different chucks—each with its own role in the process.
Top Left: The standard chuck that came with the lathe. Solid and straightforward, it does what it needs to—especially during rough turning or cleanup work.
Bottom Left: A dependable face plate (minus the wood) that I often use when I’m sanding or finishing blanks. Simple but effective.
Top Right: A keyless drill chuck—great for drilling precise, centered holes during pen making. No wrenches, no fuss—just quick swaps and a good grip.
Bottom Right: A small WEN chuck, perfect for lighter tasks or when I need a finer touch. Not bad for a tool that doesn’t take up much space.
Each of these has earned its place on my bench. They may not look fancy, but they’ve helped me shape dozens of pens—each one different, each one holding its own quiet story.
Below are pen turning mandrels. Top, called turn between centers. Middle, is my main pen mandrel. Bottom is another mandrel I use for different stages depending on what I'm turning.
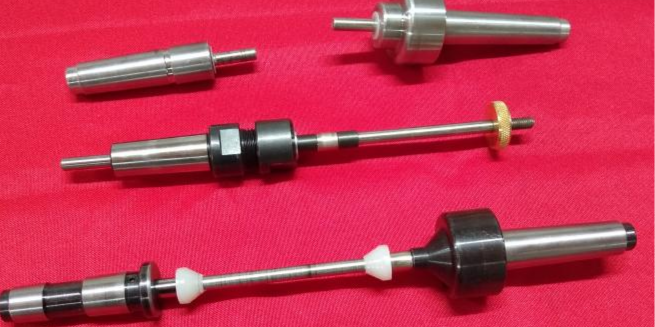
Below right is a closed end chuck and on the left is for bottle stoppers, ice cream scoops, and other similar turnings.

More Than Tools
I believe the best work happens when tools become extensions of your hand—and when the space you're in supports the work you're doing. My workshop isn't a showroom. It's filled with the smell of wood, the feel of sawdust, and the satisfaction of small, steady progress.
And in the middle of it all, these tools—simple, reliable, and well-used—help turn raw blanks into meaningful gifts.
Curious About the Process?
Every item I make starts right here—on this lathe, with these tools, in a workshop just steps from the mountain view.
If you’d like to see more behind-the-scenes glimpses of my process or learn how I choose materials and finishes, I’d love for you to stick around. Browse the shop, check out a few one-of-a-kind pens, or just reach out and say hello.
Until then, thanks for visiting the workshop.
— Mountain View Turnings
Comments